Pilot system for selecting the most cost - effective solution
Oxidation of organic materials is a process where organically polluted air is filtered through a system with a high-temperature combustion cell. The high temperature in the cell incites a reaction between the organic pollutant with the oxygen in the air called Combustion. The products of the said reaction are CO2 (Carbon Dioxide) and water considered harmless and can be vented into the atmosphere.
A factory for manufacturing hygiene products uses organic solvents intensively, as they are an integral part of the various production processes at the factory. The combination of organic solvents and high manufacturing temperatures caused a high emission rate of Volatile Organic Compounds (VOC) to the atmosphere. When the new clean air law came into effect, the Ministry of Environmental protection demanded the factory will construct a system for collecting and treating organic emissions from the production process.
ABP Chemical engineering and Ventilation Ltd. offered the factory several solutions for meeting the ministry’s requirements. The offer contained several stages:
Stage One
ABP Chemical engineering and Ventilation Ltd. engineers arrived at the factory and mapped out the emission points for the organic pollutants that will eventually connect into the treatment system. Furthermore, process information was then gathered regarding the different organic solvents and work regimes around the factory. The information was then used to conduct energy and material balance and theoretical calculations to determine the specific requirements from the regenerative thermal oxidizer (RTO).
After collecting the data and preforming the appropriate calculations, a “pilot” system was designed to collect gasses from the production processes in order to verify the calculation. The pilot system was designed to be integrated into the overall collection array in order to stay within the project’s budget.
Stage Two
High moisture and particle drift causes plugs and corrosion within the system and, over time, will increase the fuel consumption for heating the gas flow, frequent maintenance due to an increased rate of wear and tear, and overall lower treatment effectiveness. Altogether, thismade the standard RTO system ineffective for the factory. In order to prevent those problems, it was decided to add several stages to the RTO system for its protection. The stages included a gas flow dehydrator to reduce the relative moisture and a cyclonic droplet separator to prevent particles and droplets from entering the system.
Stage Three
ABP Chemical engineering and Ventilation Ltd. engineers arrived at the factory to prepare and design the ducts layouts. The main emphasis in the design was:
- Prevention of cross-contamination between different production processes.
- Designing a duct route that will allow a simple way of flow regulation.
Preventing ,as much as possible, interruption with the production process.
With the completion of the gas flow characterization, the collection layout and its challenges, ABP Chemical engineering and Ventilation Ltd. presented the plant with a report outlining all the gathered information with a recommended system necessary to meet the Ministry of Environmental protection’s requirement.
Stage Four
After the approval of the outlining report by the factory’s professional staff, ABP Chemical engineering and Ventilation Ltd. reached out to the German company “DURR,” one of the world’s leading companies for production and supply of Regenerative Thermal Oxidizers (RTO). ABP Chemical engineering and Ventilation Ltd. oversaw the purchase, delivery, transport, and setup processes on the factory grounds.
Stage Five
After installing the Oxidation and emission collection systems, the system underwent a test run in order to check for: Regularity of procedural parameters, the effectiveness of emission collection from the production processes, and the system’s compliance with the determined emission values regardless of the type or stage of the production process.
An average of less than 10 mg/m3 per
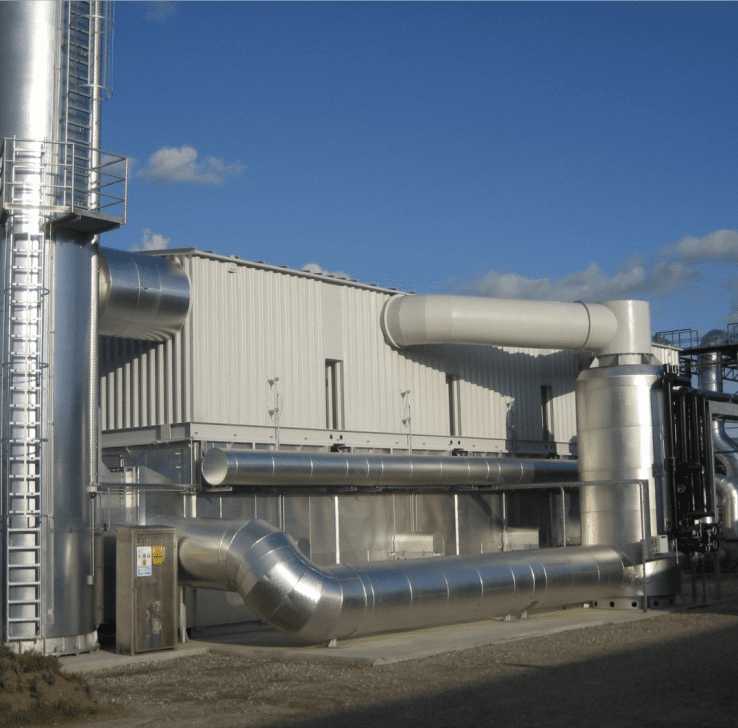